Talc Powder For Engineering Plastics
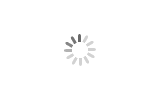
- FuTai
- LiaoNing, China
- Prompt delivery
- 3000T per month
1. Talc Powder For Engineering Plastics has feature of high DOP, stable color Gardner and easy color matching.
2. Adding our talc Powder For Engineering Plastics to plastic can effectively improve the molding shrinkage rate of plastic products, thereby improving the surface properties of the product.
3. Adding our talc powder for plastic modification to polyethylene and polypropylene plastics can effectively improve the surface hardness and surface scratch resistance of products.
4. The content of talc applied to modified plastic can increase the tensile strength within a certain range.
5. Our engineering plastic grade talc powder can make plastic’s strength, shock resistance, heat resistance, hardness and ageing resistance more homogeneous.
Introduction of talc powder for engineering plastics:
Engineering plastics is one kind of industrial plastic which can be used in materials of industrial elements or hulls. Using talc powder for engineering plastic, the plastic material can be used instead of metal structure in many applications, and applied to many different industries, by injection molding, blow molding, extrusion sheet, foaming. Based on the increasing demand, we process engineering plastic grade talc powder with high quality talc raw materials.
As an additive, modifier or filler, talc powder has been widely used in plastics, coatings, paint, ceramics, cosmetics, rubbers, papermaking, agriculture, food, medicine and other industries. Talc has the advantages of soft texture, low abrasion, high gloss, low oil absorption, and good transparency.
Product features:
Futai Talc powder for engineering plastics is produced strictly according to this industry’s physical and chemical properties. By using high grade talc material, we mainly produce highly micronized size talc powder, with features of the high DOP, stable color Gardner and easy color matching. The high content of silicon dioxide can improve the tensile strength and impact Strength of the products. The high fineness can improve the dimensional stability of products. It can promote advantages of engineering plastics during plastic modification.
Talc powder for engineering plastics offers greater strength and/or weight-savings, greater dimensional stability and flame retardation, extraordinary softness reduces machine-wear during processing, exceptionally high degree of whiteness for maximum brightness.
China is the world's largest producer, consumer and exporter of talc. With the continuous improvement of people's performance requirements for plastic products, the demand for talc powder in the plastic industry is increasing.
Main uses of talc powder for engineering plastics:
Polyoxymethylene (Polyformaldehyde)
Polycarbonate
Glycol-modified PET; Copolyesters
Polyphenylene oxide-usually modified
Polybutylene terephthalate
Wear-resisting engineering plastics
Conductive modified engineering plastics
Radiation kind of modification engineering plastics
Preliminary dyeing modification engineering plastics
General parameters of talc powder for engineering plastics:
Mesh | 1250-5000mesh |
Whiteness | above 90%-95% |
SiO2 | 55-60% |
We recommend our regular models FT2092, FT3092, FTJ1250, 9715, 9725 to the customers who use talc powder for plastic modification for plastic processing.
We can also supply according to customized quality demand.
Some precautions for using talcum powder:
To achieve the best results, use good talc powder, pay attention to the following points:
1. Talc powder must be subjected to surface activation treatment. The surface activation treatment of talc powder is mainly to improve the compatibility between talc powder and plastic raw materials and increase the modification effect. Different surface treatment agents should be selected for different plastics, such as Maleic anhydride grafted polypropylene is a good way.
2. The dispersibility of talc in plastic raw materials. Under the same formula, the dispersibility of talc in plastic raw materials has a great influence on the final physical and chemical properties of the modified material. It should be strictly controlled in the production process to affect the dispersibility of talc in plastics. The main factors of dispersibility in raw materials are formula, temperature, output, technological process, etc. In addition, when the amount of talc added is large, a step-by-step method can be adopted to achieve a good dispersion effect.
3. For different plastics, different specifications of talc should be selected to achieve the desired effect. This is very particular, and a bad choice may backfire. Because different plastics, different products, and different conditions of use have different requirements on raw materials, different choices must be made to achieve the desired effect.
About our company:
Dalian Futai Mineral New Materials Technology Founded in 2009, the company is a comprehensive enterprise integrating mining and processing of mineral products, R & D and production of masterbatch, product sales and service. Since its establishment, the company has been committed to the processing of talcum powder and related filler masterbatch, and has won unanimous praise in the industry. It is a professional technical production enterprise and has won a number of awards from relevant associations in the industry.