Talc Powder in Tiles
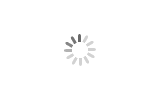
- FuTai
- LiaoNing, China
- Prompt delivery
- 3000T per month
Highlights
1. Talc powder in tiles improves thermal shock resistance of ceramics and reduces fractures.
2. Tiles grade talc powder imparts great after burning whiteness to ceramics.
3. Talc for porcelain tiles makes ceramics acid resistant.
4. Talc powder in tiles is hydrophobic in nature. Therefore, it helps to prevent water leakage and seepage in sanitarywares.
5. The grinding process of talcum powder is highly customizable. Thus, it is possible to achieve the desired particle size best suitable for each type of ceramic product rather than one size fits all.
Introduction of Talc powder in tiles:
Tiles grade talc powder is a catalyst in the ceramic industry and has a high temperature resistance. In general, the addition of talc powder has positive effects to ceramic, for example it increases the mechanical and optical properties of the ceramic material and glazes. Through the addition of talc, the properties of the ceramic product can be changed and the combustion temperature is reduced. This has a positive effect on the production costs.
Effects and benefits:
★ Increased thermal shock resistance and reduced fractures
★ Improved whiteness and acid resistance
★ Stabilizing of pyroplastic distortion (thermal expansion and firing contraction)
★ Improvement of density and stability
★ Reduction of cracking
★ Reduction of firing cycles and processing temperature
★ Increased resistance
Main uses of Talc powder for ceramics:
For tiles
For sanitary wares
For tableware and artware
For industrial ceramics
General parameters of Talc powder in tiles:
Mesh | 325 – 2000 mesh |
Whiteness | above 94%-98% |
SiO2 | 35-62% |
We have different models of talc powder for tiles. For more info about the products, please feel free to contact our technician representatives.
We can also supply according to customized quality demand.
Some precautions for using talcum powder:
Talc is the softest mineral in the world. Talc is a hydrated magnesium sheet silicate with the chemical formula Mg3Si4O10(OH)2. The elementary sheet is composed of a layer of magnesium-oxygen/hydroxyl octahedra, sandwiched between two layers of silicon oxygen tetrahedra. The main or basal surfaces of this elementary sheet do not contain hydroxyl groups or active ions, which explains talc's hydrophobicity and inertness.
Although all talc ores are soft, platy, water repellent and chemically inert, no two talcs are quite the same. Futai talc products range from varied whiteness, particle size and purity. Talc is a vital part of everyday life. The magazines we read, the polymers in our cars and houses, the paints we use and the tiles we walk on are just some of the products that talc enhances.
Using of right talc for the right industry enhances the end use product. Our talc products range from varied whiteness, particle size and purity. All our range of industrial talc's are asbestos free and are manufactured in whiteness range starting at 86% to 98% Whiteness and available in the mesh size of 325 to 3 microns. The talc is suitable for paints and coatings, rubber, wires and cables, polymers and plastics, ceramics, cosmetics and pharmaceutical Industry.
Company Profile
Founded in 2009, Dalian Futai Mineral New Material Technology Co., Ltd. is a comprehensive enterprise integrating mining and processing of mineral products, R & D and production of masterbatch, product sales and service, formerly known as Yingkou Jintong New Material. Since its establishment, the company has been committed to the processing of talcum powder and related products masterbatch, and has won unanimous praise in the industry. It is a professional technical production enterprise and has won a number of awards from relevant associations in the industry.
Company Resources
The company invests in the exploitation of a talc mine with explored reserve of 800,000 tons and a planned annual mining volume of 50000 tons. It integrates two processing plants, including 4 Airjet millers, 2 Raymond millers and 1 vertical roller grinder, with an annual production capacity of 50000 tons of powder.
In addition, the factory is equipped with 3 twin-screw granulation production lines, 1 non-carrier granulation production and drying line, which can customize and process various masterbatch products according to different needs of customers from domestic and overseas.